The Company Bottleneck – Identifying & Removing Constraints
A company with a complex, multi-step production process struggled with bottlenecks, inefficient trial-and-error improvements, and limited visibility into key constraints like cycle times and downtime. These issues restricted throughput and hindered overall performance improvements.
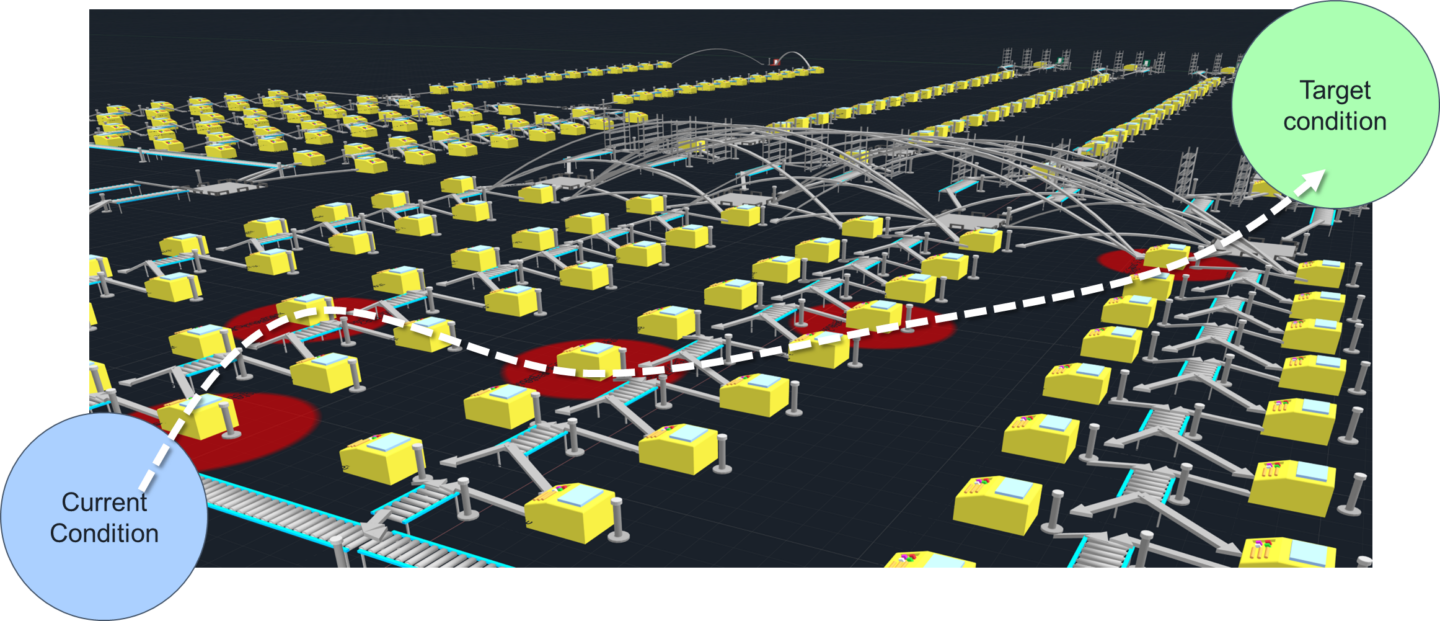
Challenge
A company struggling with 50+ production steps faced:
- Bottlenecks in production flow, leading to inefficiencies.
- Trial-and-error approaches (Kata) without real improvements.
- Limited visibility into constraints, such as cycle times, availability, downtime, and setup times.
Solution
Using Simulation-Based Constraint Removal (SCORE) in FACTS Analyzer Professional*, the company:
- Identified 7 key improvements that significantly increased throughput.
- Used optimization tools to pinpoint exact constraints impacting performance.
- Replaced manual trial-and-error with data-driven optimization strategies.
Results
- Identified the necessary steps to increase throughput by 50%.
- Precise constraint identification, reducing inefficiencies.
- A structured path toward production improvement, rather than guesswork.
Conclusion
With SCORE optimization in inFACTS Studio, the company eliminated production constraints, increased throughput, and transitioned to a more structured, data-driven improvement process.
*FACTS Analyzer was the previous generation of inFACTS Studio, built on a 2D environment.
NOTE: current SCORE functionality to automate the construction of optimization problems are soon to be ported and integrated into the inFACTS Studio.